In recent years, under the influence of carbon emission pressure, the policy support for new energy vehicles in various countries has continued to strengthen. The share of new energy vehicles in the overall automotive market has been increasing year by year. The most important component of new energy vehicles is the power battery, so the market competition for lithium batteries is becoming increasingly fierce. Power batteries are composed of individual battery cells, so quality control is necessary for each cell.
Today, we will introduce the application case of Yishi Technology's LVM series cameras in the lithium battery industry!
2.1 Inspection of welding seams on the top cover of battery cells: missed welding, excessive height, and welding holes
Customer: Global leading enterprise in the new energy lithium battery industry
Workpiece: An internationally renowned new energy vehicle battery cell
Downstream industry: New energy battery industry
Product model: LVM-2610
Technical requirements: Inspect the welding quality of the top cover of the battery cell (such as missed welding, virtual welding, protrusions, explosion points, explosion points, knife marks, etc.);
Customer value: achieving fully automated detection; Improve product quality, prevent defective products from flowing out to the vehicle factory, and avoid serious quality accidents; Improve the consistency of detection results.
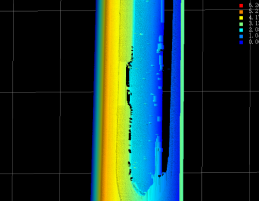
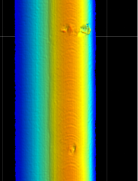
(Point Cloud Map)(Point Cloud Map)
2.2 Appearance inspection of pre coating battery cells: defects such as dents and scratches
Customer: Global leading enterprise in the new energy lithium battery industry
Workpiece: An internationally renowned new energy vehicle battery cell
Downstream industry: New energy battery industry
Product model: LVM-2630
Technical requirements: Detect defects such as dents and scratches on the appearance of battery cells;
Customer value: achieving fully automated detection; Improve product quality, prevent defective products from flowing out to the vehicle factory, and avoid serious quality accidents; Improve the consistency of detection results.
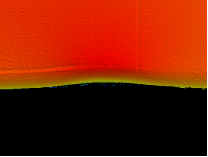
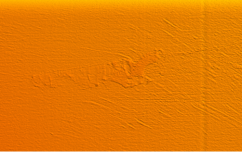
(Dents)(Scratches)
2.3 Surface defect detection of battery cells after coating
Customer: Global leading enterprise in the new energy lithium battery industry
Workpiece: An internationally renowned new energy vehicle coated battery cell
Downstream industry: New energy battery industry
Product model: LVM-2630
Technical requirements: Two LVM2630 splicing methods shall be used for inspection to analyze defects such as foreign objects, scratches, wrinkles, pits, bubbles, etc; Customer value: achieving fully automated detection; Improve product quality, prevent defective products from flowing out to the vehicle factory, and avoid serious quality accidents; Improve the consistency of detection results.
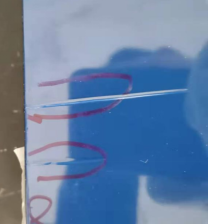
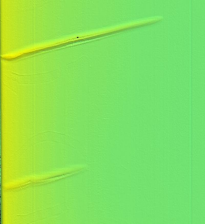
(Physical image)(Point cloud image)
2.4 Busbar post weld quality inspection
Customer: Global leading enterprise in the new energy lithium battery industry
Workpiece: Busbar cell module
Downstream industry: New energy battery industry
Product model: LVM-2520
Technical requirements: 3D camera paired with 2D camera to detect the quality of Busbar after welding;
Customer value: achieving fully automated detection; Improve product quality, prevent defective products from flowing out to the vehicle factory, and avoid serious quality accidents; Improve the consistency of detection results.
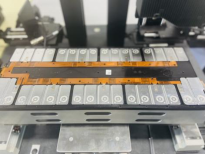

(Physical image)(Point cloud image)
2.5 PACK foreign object detection
Customer: Global leading enterprise in the new energy lithium battery industry
Workpiece: PACK box
Downstream industry: New energy battery industry
Product model: LVM-2630
Technical requirements: Detect foreign objects of the same color and calculate the depth of the foreign object based on the detection;
Customer value: achieving fully automated detection; Improve product quality, prevent defective products from flowing out to the vehicle factory, and avoid serious quality accidents; Improve the consistency of detection results.
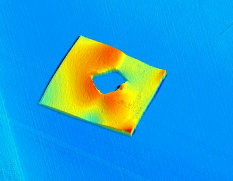
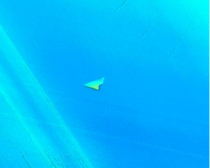
(Point Cloud Map)(Point Cloud Map)
1) A full range of product lines with independent intellectual property rights: high-precision, high-speed, and highly stable 3D cameras, with performance indicators reaching international first-class level, measurement repeatability accuracy within 0.1 micrometers, and scanning speed up to 56000Hz;
2) Having industry-leading 3D vision solution capabilities: a powerful algorithm system that can be used for multi-channel point cloud data stitching, helping customers achieve technological innovation;
3) Rich application scenarios: Customized 3D cameras can be provided to meet various on-site detection and measurement environments. Currently, they have been widely used in consumer electronics, new energy batteries, automotive manufacturing, sheet metal processing and other fields.
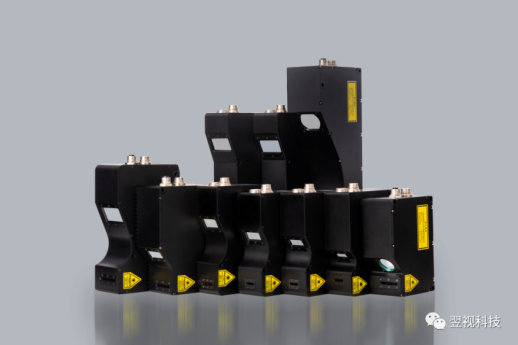