Background knowledge
In the current era where automotive safety is of utmost importance, the quality control of brake pads is a crucial link that cannot afford to be neglected. Traditional detection methods are often limited by two-dimensional perspectives and subjective judgments, and it is difficult to meet the pursuit of high precision and high efficiency in the modern automotive industry. The 3D camera technology came into being, opening a new chapter in the detection of automotive brake pads.
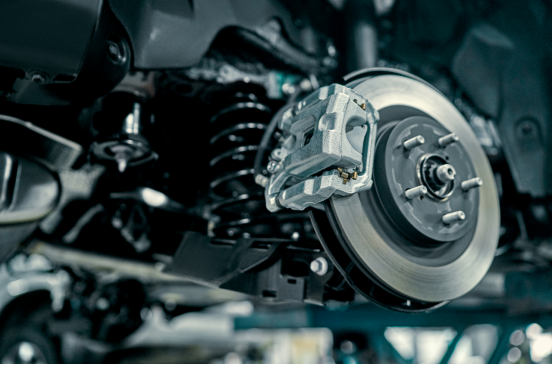
Camera selection
Today, I would like to introduce to you the application case of Yishi Technology's LVM2040 linear laser 3D camera in the automotive industry inspection!
LVM2040 3D intelligent sensor. Its full-frame acquisition rate is 340Hz. With the setting of ROI, it can reach up to 10000Hz. There are 2048 physical contour points. Under the condition of uniform spacing sampling of the depth map, it can reach up to 4096 points. It meets the needs of various high-speed and large-batch detection applications. It is a high-performance-to-price ratio 3D intelligent sensor!
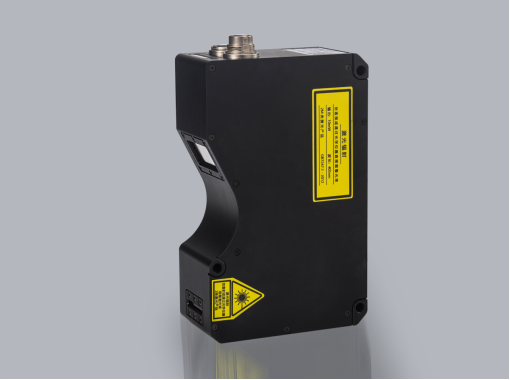
Detection item
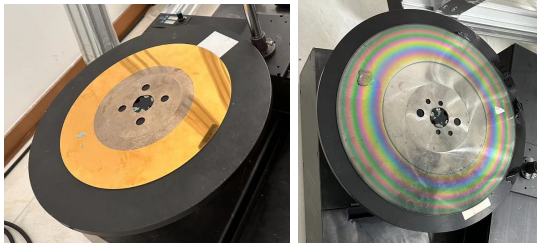
Workpiece information
·Material: Metal, with texture and reflective.
·Color: Yellow and colorful.
·Size: The large disc has a diameter of 300mm, and the small disc has a diameter of 250mm.
Detection requirements
· Penetrate grease and measure the flatness of the metal disc. The accuracy requirement is 0.2mm.
· Finish scanning one disc surface within 10 seconds.
· Take points for measuring the flatness matrix. The points can be taken according to a 1-5mm matrix (requiring that each point is the actual height value of the disc surface).
Detection environment and installation methods
· Scanning method: The camera is fixed, and the test specimen moves along the central straight line for scanning and measurement.
· Triggering method: Using encoder triggering to output a stable AB phase differential signal.
· Communication method: TCP/IP Ethernet.
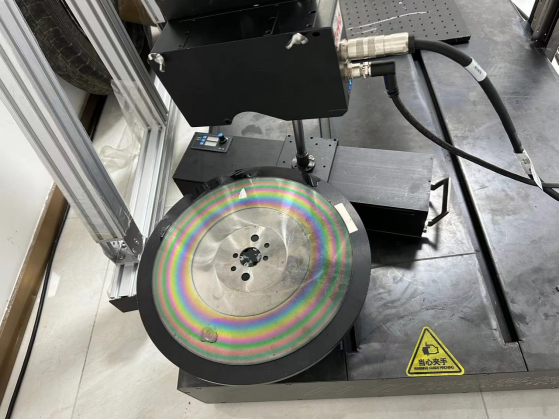
Image acquisition effect
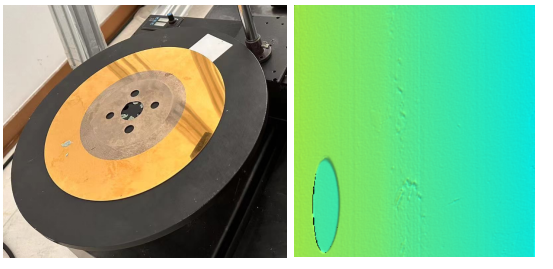
·The picture shows physical pictures and some point cloud pictures.
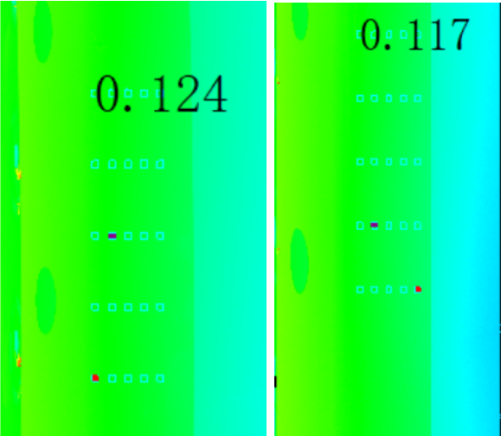
·The picture shows the flatness data of the small disc after applying grease and the flatness data of the small disc after wiping off the grease.
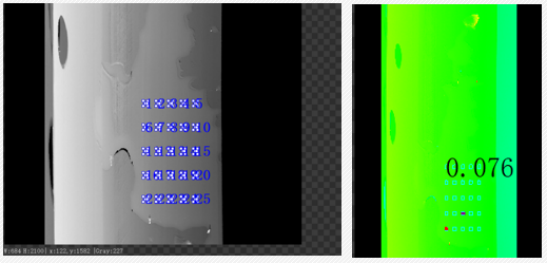
·The picture shows the data diagram of the flatness of the large disc coated with grease.
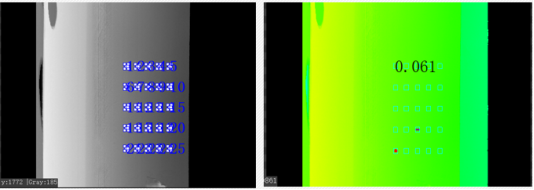
·The picture shows a large disc for erasing grease flatness data.
Detection conclusion
·Penetrating grease and measuring the flatness of the metal disc. The accuracy requirement is 0.2mm. Judging from the test data, the flatness difference of the small disc before and after applying grease is 0.006, and the flatness difference of the large and small discs before and after applying grease is 0.015.
·Scanning one disc surface within 10S. The test scanning speed is that it can be completed within 5S.
·Measuring the flatness matrix and taking points. Points can be taken according to a 1-5mm matrix. Each point needs to be the true height value of the disc surface. The requirements for taking points can be tested according to customer requirements.