Background knowledge
As a key carrier of electronic components, ceramic substrates are widely used in the fields of electronic power, semiconductors, etc. Their quality directly affects the performance and reliability of electronic devices. With the increasing requirements for the accuracy and quality of ceramic substrates in the industry, traditional detection methods are gradually difficult to meet the needs. 3D cameras play an important role in the detection of ceramic substrates with their unique advantages, promoting the development of detection towards automation and high precision.
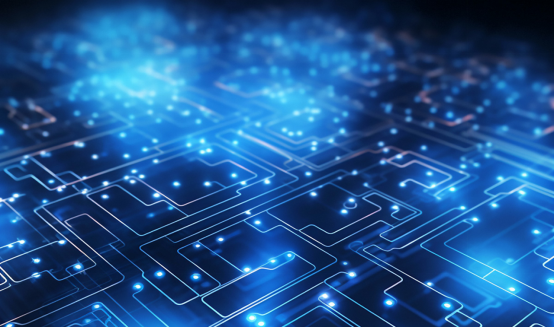
Camera Selection
Today, I will introduce an application case of the LVM2520 line laser 3D camera of Next Vision Technology in the 3C industry!
The LVM2520 3D intelligent sensor has a full-frame acquisition rate of 2500Hz, which can reach up to 56000Hz by setting the ROI; the physical contour points are 1920 points, and it can reach up to 4096 points under the condition of uniform spacing sampling of the depth map, which is ideal for 3D detection of small parts and is an ideal choice for high-speed online detection systems.
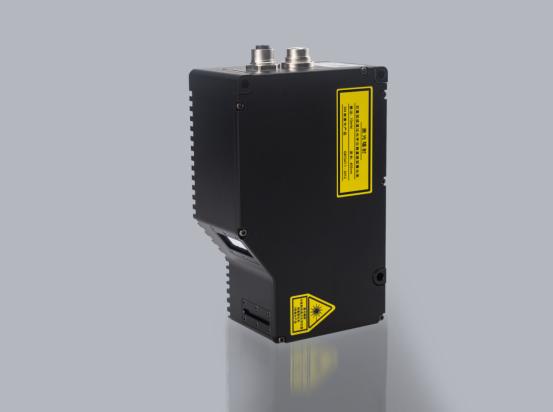
Test item
·Level difference between the yellow area and the white ceramic bottom
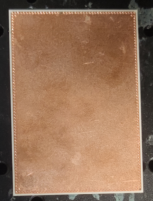
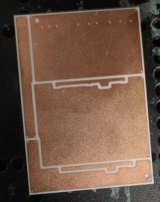
Detection Environment and Installation Method
· Scanning Method: The camera is fixed, and the test sample moves along the central straight line for scanning measurement.
· Triggering Method: Encoder triggering is adopted to output a stable AB-phase differential signal.
· Communication Method: TCP/IP Ethernet

Picture-taking effect
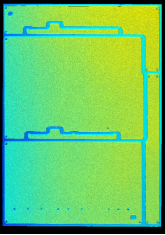
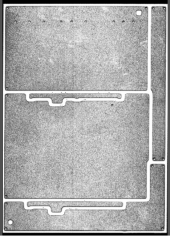
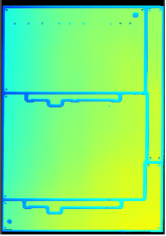
Positive point cloud effect diagram
*The figure shows a point cloud map, a brightness map, and a depth map
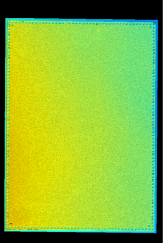
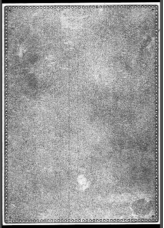
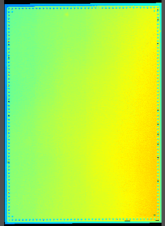
Reverse point cloud effect diagram
*The figure shows the point cloud diagram, brightness diagram, and depth diagram.
Measurement data
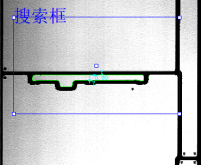
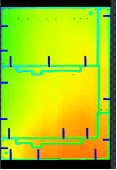
The figure shows the feature point positioning and extraction points, and calculates the segment difference.
*Based on the depth image collected by the camera, through preprocessing, grab the contour feature points of the product and position them; through contour detection, calculate the segment difference from the yellow area of the product to the white ceramic bottom, and test the static data of 17 segment difference points.
Data analysis
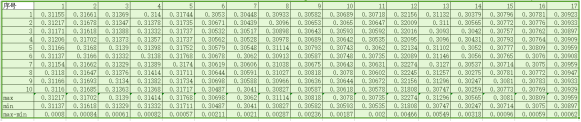
17 points, measure 10 groups of dynamic data, with a maximum repeatability within 0.01 mm
Test Conclusion
· The imaging effect of this solution is relatively complete, and the static repeatability within 10 times is within 0.01 mm, meeting the customer's test requirements.