Background knowledge
As the core power source of various electronic devices and new energy vehicles in modern society, the quality and safety of lithium batteries are of crucial importance. The weld seam, as a key connecting part in the production of lithium batteries, directly affects the performance, lifespan, and even the safety of use of the batteries. When faced with complex defects in lithium battery weld seams, traditional detection methods often show deficiencies such as low efficiency and poor accuracy. With the development of industrial automation and intelligence, 3D industrial cameras have emerged in the field of lithium battery weld seam defect detection due to their unique three-dimensional imaging and high-precision measurement capabilities, providing a new and powerful way to ensure the quality of lithium batteries.
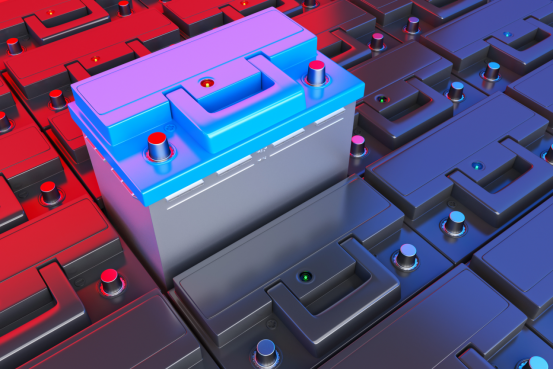
Camera Selection
Today, I would like to introduce an application case of the LVM2520 line laser 3D camera of Next Vision Technology in the new energy industry!
The LVM2520 3D intelligent sensor has a full-frame acquisition rate of 2500Hz, which can reach up to 56000Hz by setting the ROI; the number of physical contour points is 1920 points, and it can reach up to 4096 points under the condition of uniform spacing sampling of the depth map, which is used for 3D detection of micro parts and is an ideal choice for high-speed online detection systems.
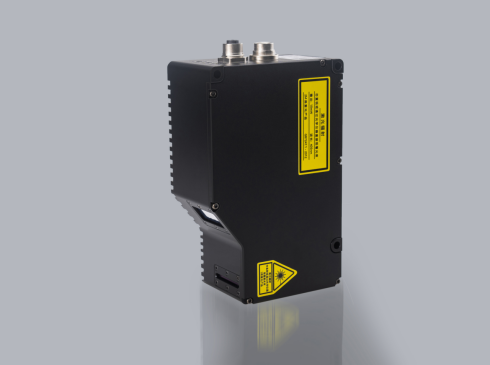
Test item
·Defect detection of lithium battery welds (product length: 140mm * width: 25mm)
Testing environment and installation method
· Scanning method: The camera is fixed, and the test sample moves along the central straight line for scanning measurement.
· Triggering method: Encoder triggering is adopted to output a stable AB differential signal.
· Communication method: TCP/IP Ethernet
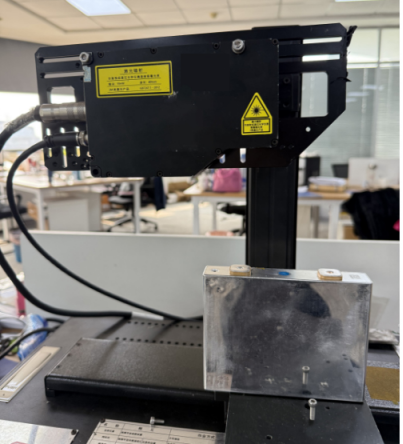
Imaging effect
· Point cloud map - long side


·Point cloud map - Weld seam OK
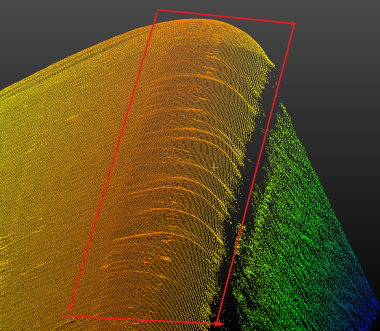
·Point cloud map - Short side OK
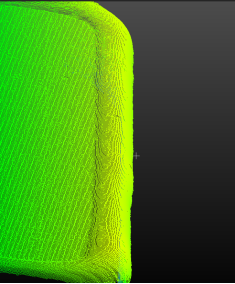
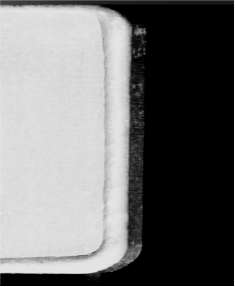
Defect identification
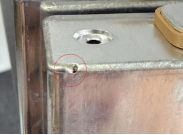
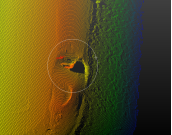
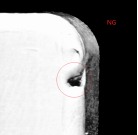
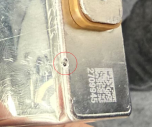

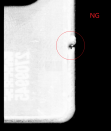
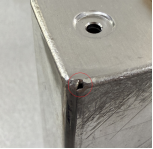
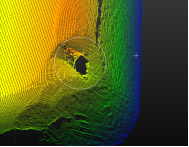
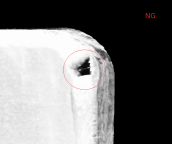
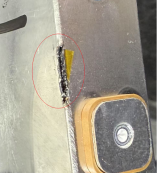
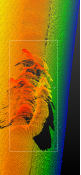
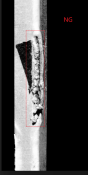
·The above pictures are respectively the physical picture - point cloud picture - brightness picture. By analyzing the spots in the brightness picture, it can be judged as NG if the black pixels exceed the set range.
Test conclusion
· The imaging effect of this scheme is relatively complete, and defects above 0.16mm × 0.16mm can be accurately detected through algorithms.